When selecting swage hose fittings suitable for high-pressure applications, several factors need to be considered to ensure safety, performance, and reliability:
Pressure Rating: High-pressure applications necessitate meticulous attention to pressure ratings when selecting swage hose fittings. Conduct a thorough analysis of the operating pressure within your system, considering potential pressure spikes or fluctuations. Ensure the chosen fittings possess pressure ratings that comfortably exceed the anticipated operating pressures, providing a safety margin to mitigate the risks of fitting failure or leakage.
Material Strength: The inherent strength and durability of the materials comprising swage hose fittings are critical determinants of their performance and reliability in high-pressure applications. Evaluate the mechanical properties of candidate materials, including tensile strength, yield strength, and resistance to fatigue and corrosion. Stainless steel and high-grade alloys are favored choices renowned for their exceptional mechanical properties and corrosion resistance, ensuring performance and longevity under the rigors of high-pressure operation. Consider environmental factors, such as exposure to corrosive fluids or harsh operating conditions, when assessing material suitability to safeguard against premature degradation or failure.
Compatibility: Achieving compatibility between swage hose fittings, hoses, and conveyed fluids is imperative for maintaining system integrity and operational efficiency in high-pressure environments. Conduct a comprehensive assessment of material compatibility considerations, accounting for potential chemical reactions, material degradation, or dimensional discrepancies that may compromise fitting performance or longevity.
Sealing Mechanism: The effectiveness of the sealing mechanism employed by swage hose fittings is paramount in preventing fluid leakage and ensuring system integrity under high-pressure conditions. Evaluate the design and performance characteristics of the sealing arrangement, prioritizing fittings equipped with robust sealing mechanisms engineered to withstand the demands of high-pressure operation. Precision-engineered O-ring seals, metal-to-metal seals, and advanced sealing technologies offer reliability and resilience against pressure-induced leaks, minimizing the potential for fluid escape and system downtime.
Fitting Design: The design intricacies and structural robustness of swage hose fittings significantly influence their ability to withstand high-pressure environments and maintain reliable connections. Prioritize fittings characterized by robust design features, such as reinforced body structures, optimized stress distribution, and secure attachment mechanisms, to minimize vulnerability to pressure-induced failure or deformation. Conduct thorough evaluations of fitting designs, considering factors such as material thickness, geometry, and surface finish, to identify fittings capable of withstanding the mechanical stresses inherent in high-pressure applications.
Installation Requirements: Proper installation practices are fundamental to achieving secure and leak-free connections in high-pressure hose assemblies, necessitating adherence to recommended procedures and protocols. Familiarize yourself with the specific installation requirements associated with swage hose fittings, including the use of specialized swaging equipment, fitting assembly techniques, and torque specifications. Train personnel responsible for fitting installation to ensure competency and compliance with established installation procedures, minimizing the risks of fitting-related issues and enhancing system reliability. Implement stringent quality control measures to verify fitting integrity and alignment post-installation, mitigating potential sources of fitting-related failures or leaks that may compromise system performance and safety.
Coupling For SAE 100R1AT 2SN Shock-absorbing Removable Hose
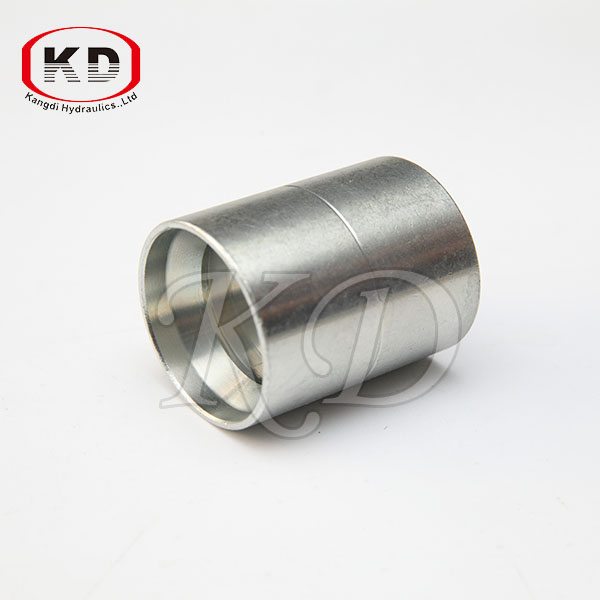
A Coupling For SAE 100R1AT 2SN Shock-absorbing Removable Hose is a specialised piece of device designed to mitigate the effect of vibrations and shocks in numerous industrial programs. Constructed with advanced materials, these hoses are engineered to take in and deplete the energy generated with the resource of surprising movements or vibrations in equipment and piping structures. The detachable characteristic allows for easy preservation and substitute, ensuring top of the line overall performance over an extended period.