Solving common problems with interlocking hose joints like leaks or joint failures involves several steps:
Identify the Problem: Conduct a comprehensive assessment of the interlocking hose joint to pinpoint the exact nature of the issue. Utilize visual cues such as discoloration, pooling liquids, or audible hissing sounds to detect potential leaks. Employ tactile inspection techniques to detect irregularities in surface texture or temperature variance, indicative of joint failures or compromised seals.
Inspect the Fittings: Engage in a meticulous examination of the interlocking hose fittings, employing magnification tools if necessary to detect minute imperfections. Scrutinize the entirety of the fitting's surface area, paying particular attention to high-stress regions such as threads, ridges, or compression points. Utilize precision measurement instruments to assess dimensional accuracy and confirm compliance with manufacturer specifications.
Tighten the Connections: Exercise judicious torque application techniques when tightening interlocking hose fittings, utilizing calibrated torque wrenches to achieve compression without exceeding prescribed limits. Employ rotational force in gradual increments, periodically reassessing joint integrity to prevent over-compression-induced damage. Utilize supplementary support structures or fixturing to stabilize the assembly during tightening procedures, minimizing the risk of misalignment or distortion.
Replace Seals or Gaskets: Execute a systematic disassembly of the interlocking hose joint to access internal sealing elements, observing proper handling protocols to prevent contamination or degradation. Select replacement seals or gaskets constructed from materials compatible with anticipated operational conditions, considering factors such as chemical compatibility, temperature resistance, and compression characteristics. Employ precision measuring instruments to verify dimensional compatibility and ensure a snug fit within the designated sealing grooves or interfaces.
Apply Sealant: Select an appropriate sealant formulation tailored to the specific operating parameters and materials of the interlocking hose joint, ensuring compatibility with both metallic and elastomeric components. Employ precision dispensing techniques to apply sealant in a uniform and controlled manner, mitigating the risk of excess buildup or migration into critical fluid passages. Implement curing or setting protocols specified by the sealant manufacturer to optimize bond strength and chemical resistance properties.
Check for Obstructions: Conduct a thorough inspection of internal hose passages and fitting interfaces to identify and eliminate any obstructions or foreign contaminants that may compromise fluid flow or interfere with sealing mechanisms. Utilize specialized inspection tools such as borescopes or endoscopes to access confined spaces and visually confirm component cleanliness. Employ compressed air or fluid flushing techniques to dislodge stubborn debris and restore unimpeded fluid pathways.
Inspect Hose Integrity: Perform a comprehensive visual and tactile inspection of the entire length of the hose assembly, scrutinizing for signs of external damage such as abrasions, cuts, punctures, or bulges. Utilize non-destructive testing methods such as ultrasonic thickness gauging or eddy current analysis to assess internal integrity and detect potential delamination or material degradation. Employ hose burst testing apparatus to verify compliance with specified pressure ratings and identify weak points requiring remediation.
JIC Male 74°Seal Highly secure Efficient Interlock Fittings
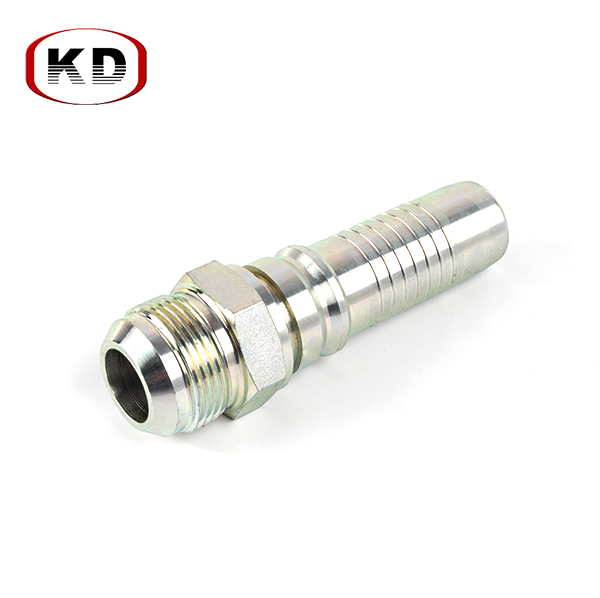
Designed with precision and engineering excellence, the JIC Male 74°Seal Highly secure Efficient Interlock Fittings offer a sturdy solution for programs demanding excessive safety and performance. The 74° seal guarantees a decent and dependable connection, stopping leaks and ensuring the integrity of fluid structures.